The SELFRAG Lab
Product description
The SELFRAG Lab system is designed as an innovative solution for the fragmentation of complex materials such as ores, electronics and other recycled materials, and is seeing increasing usage in the field of comminution and mineral processing.
The SELFRAG Lab is a laboratory-scale electrodynamic high voltage pulse power (HVP) batch processing unit. It is a standard ‘off the shelf’ HVP system and is in use in over 45 universities and research institutions worldwide. A mature technology in its second version uses patented SELFRAG high voltage pulsed power technology to electrodynamically fragment and liberate individual phases from composite materials. The system delivers a series of 90 – 200kV electric pulses up to 5 times per second (5Hz) through a material; to selectively fragment it along phase boundaries.
The system is the first of its kind to be purposely built for ease of use by operators without high voltage or electrical engineering experience. The Lab is designed for use by everyone, from undergraduate students to professors in academia, and from lab assistants to CEOs in the industry. It features a built-in touch panel where equipment settings like electrode gap, pulse voltage, pulse repetition rate/frequency, and number of pulses can be easily adjusted between a minimum and maximum set of values. The software stores user settings and processing data of the previous single batch in a digital memory system. An online connection allows fast support and help from SELFRAG- experts for troubleshooting or any other support.
All the safety-relevant systems are activated automatically and require no user interaction with critical high voltage parts. The Lab unit is self-contained to meet all EU health and safety regulations. The process chamber is a fully enclosed faraday cage to protect the user from HV power, noise and electromagnetic radiation.
The machine is safe to the touch when processing, and can be used by those with pacemakers or around other sensitive electronic IT or analytical equipment. Internal soundproofing ensures the electrodynamic system is also quiet compared to electrohydraulic systems, generating 79dB maximum during processing, meaning hearing protection is not needed.
The Lab allows the batch processing of either a single rock sample, or up to 1 kg of unconsolidated material. Two vessel designs allow for material to either be contained within the chamber, or for processed material to fall through a sieve into a collection vessel beneath. With both options, the sample is contained within a fixed space eliminating sample loss. Disassembly and cleaning of the process vessel between samples is quick and easy.
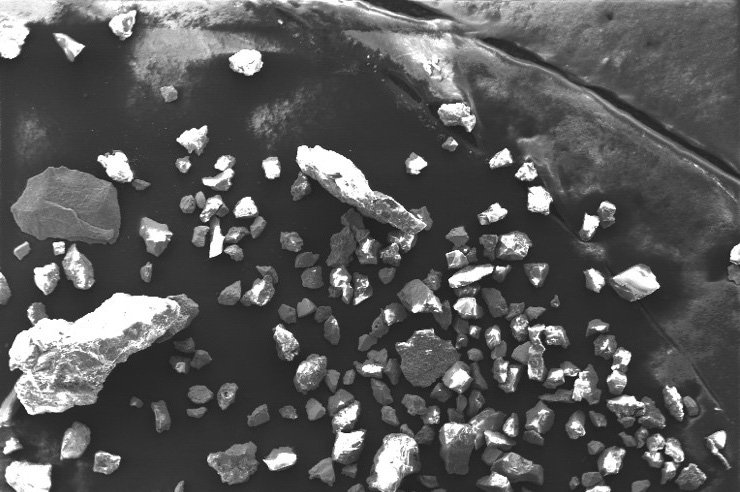
The system features space for forklift tines and lugs for crane lifting built into the frame and is easily transported on included casters to the final destination. The Lab is 0.86 m wide, 2.06 m high and 2.37 m long and is designed with consideration for access to laboratories with limited space availability. The lab must be positioned on level (or near level), solid ground with a load bearing capacity of 1 ton/m2.
The Lab system and accompanying recommended peripheral the ‘sink station’ require less than 5m2 floor space. The standard mains power requirements are 3x400V, a trafo can be supplied for other voltages. De-ionized water is recommended as process medium to achieve best results.
The SELFRAG LAB comes with a Starter Kit with all required parts for operation. After 1 day commissioning and 1 day user training, the system is ready to use by its owner.
SELFRAG has a dedicated after-sales team to support customers beyond the installation of the machine. The internet connection allows SELFRAG technicians to examine the process history of the lab and run diagnostics remotely.
SELFRAG technicians are also available to consult via email, phone, or on-site. An annual service of the equipment is recommended to ensure proper operation. Service contracts are available from SELFRAG.
High Purity Sizing Equipment
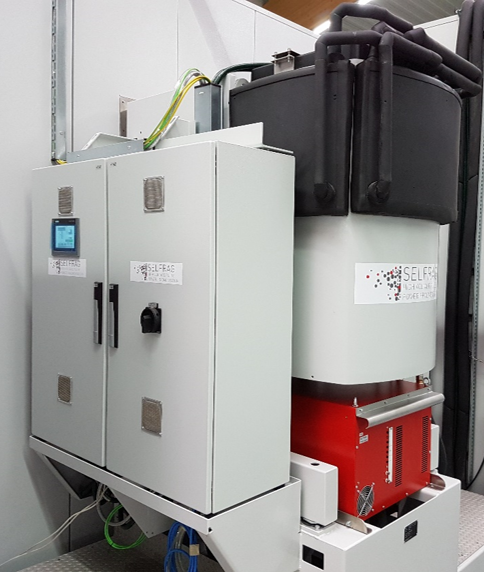
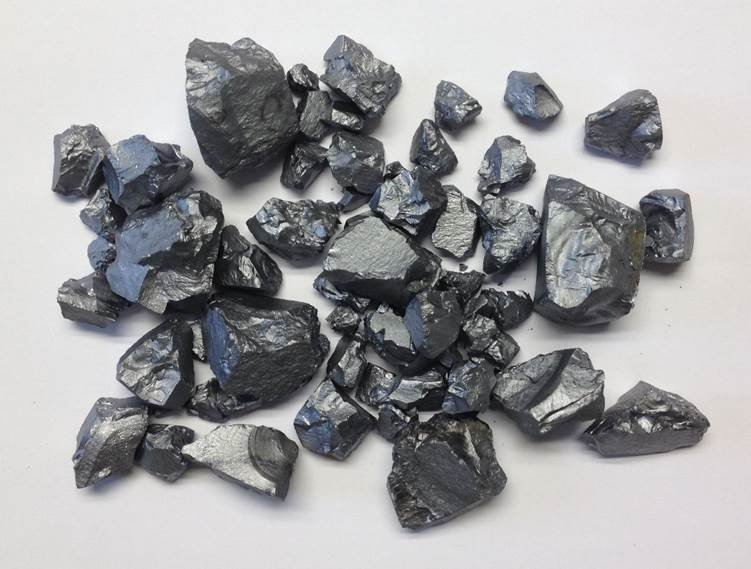
Product description
The innovative SELFRAG product - High Purity Crusher -is the only solution worldwide which offers a touchless crushing method for high purity materials such as poly-or monosilicon and glass.
With the first units installed already in 2016, the industrialized and patented HVP-Generators are a key part of electronic grade polysilicon crushing lines at the leading producers around the world.
In one step and fully automated, it crushes rods or large pieces into the required size classes by means of HVP. Followed by sieving, drying, etching and bagging steps, the crushing process can be fully automated. Compared to manual crushing methods, a significant cost saving can be achieved.
The touchless size reduction allows lowest contamination levels due to fragmentation with electric pulses and electrodynamic effects in a Di-water bath.
The user selectable size distribution (2 – 150 mm range) provides optimized yields, depending on the production needs, while keeping the product losses at a very low level.
Annual throughputs of up to 8’000 t.p.a. are achieved with only 1 SELFRAG HVP-generator installed. The total operation costs can be as much as 28% lower compared to any other crushing process due to an automated and efficient process.
The HVP-generators for high purity applications are customized units, engineered and integrated into production lines of our clients according to their individual needs.
Please contact us directly for more information or inquiries: info@selfrag.com
All the safety-relevant systems are activated automatically and require no user interaction with critical high voltage parts. The unit is built to meet all EU health and safety regulations and is CE certified.
The machine is safe to the touch when processing, and can be used by those with pacemakers or around other sensitive electronic IT or analytical equipment. Internal soundproofing ensures the electrodynamic system is also quiet compared to electrohydraulic systems, generating 79dB maximum during processing, meaning hearing protection is not needed.
The SELFRAG HVP-process generates roundish shaped chips. This leads to an excellent flowability of the particles, which is suitable for the continuous charging process of monosilicon pullers. In comparison to standard processes, the feed-in is not blocked by needle-shape particles and a denser filling grade can be achieved with the material processed by a SELFRAG Rod Crusher.
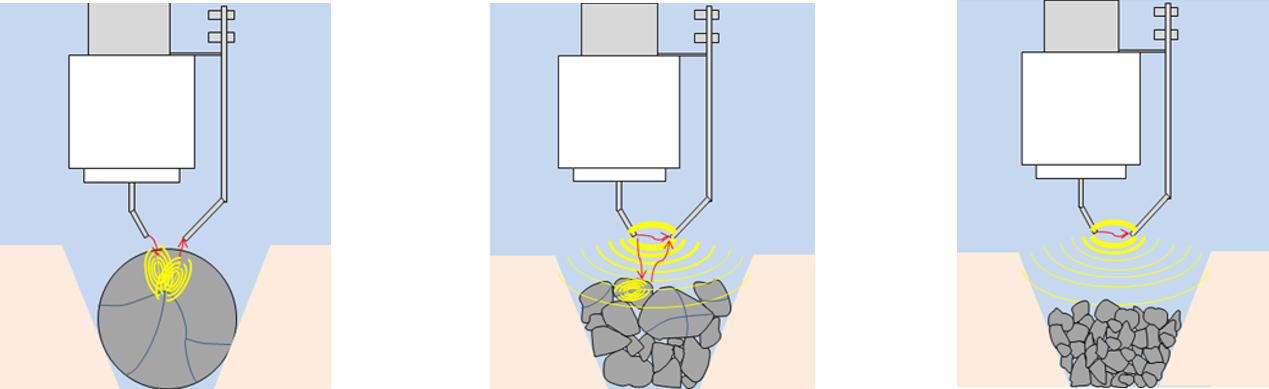
SELFRAG has a dedicated after-sales team to support customers beyond the installation of the machine.
Dedicated training, ramp-up/processing support and spare parts services are provided for our clients.